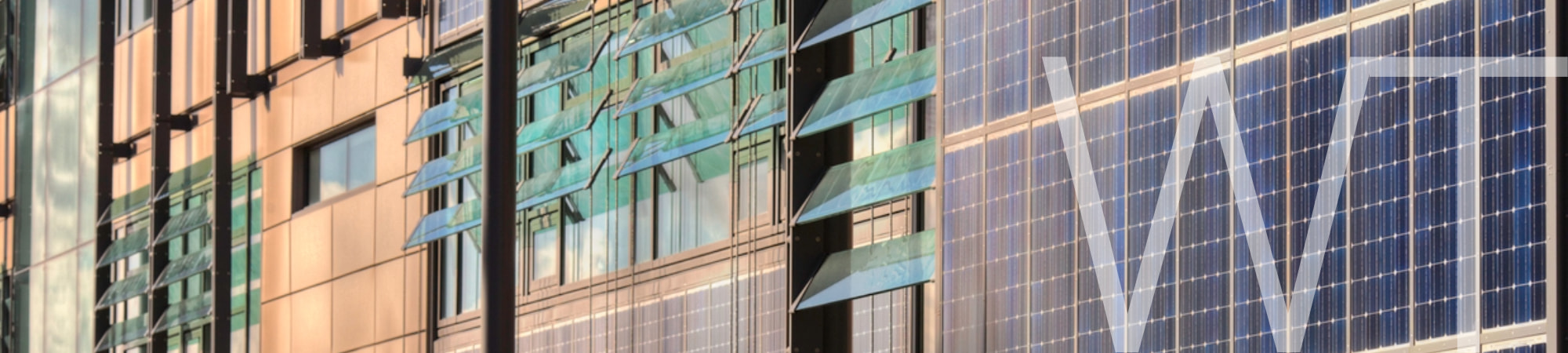
The materials in the facade of a building significantly contribute to the embodied carbon emissions ‘baked in’ before a building begins its useful life. This presents a significant opportunity for reducing embodied carbon. However, the challenge in facade design is that performance requirements are vast.
It’s expected that a building will be aesthetically pleasing (even spectacular or iconic), but also cost-effective; robust enough to stand up to and shield us from the elements, but let in plenty of daylight; be distinctive, but comply with town planning requirements; achieve fire performance, but enable entry and exit; withstand wind loadings, but allow natural ventilation… and now, alongside all these criteria, buildings must strive to achieve the lightest environmental footprint possible.
With each of these requirements, the opportunity for improvement grows. The building industry has had time to test and discover various solutions to typical performance requirements, such as what materials, components, and parameters to lean on when targeting wind loadings, value engineering, thermal or acoustics. For many in the industry, that part is almost instinctive. Now, however, the risk profile has grown to encompass a new variable, which means going outside the comfort zone and embarking on a new testing and discovery process.
Finding solutions that achieve all these often opposing goals may seem daunting, but inspiring solutions will emerge if the industry has the will to discover, test and implement them.
Consider carbon first
Methods and materials that satisfy the typical performance requirements of a facade are already very well established. The introduction of carbon reduction, however, is a new challenge and it needs to be considered early. Exploring carbon impacts in the early-stage design studies allows more flexibility to understand and test options and shift the needle while the design is still flexible enough and before any planning permissions and expectations are locked in.
It’s common sense that the ultimate ‘gold star’ solution for a lower carbon footprint will always be extending the life of existing buildings rather than building new. However, community expectations for aesthetics, stricter safety standards, and the effects of current facades on comfort and energy efficiency will likely continue driving facade upgrades, meaning the carbon challenge will persist.
Optimise and cherry pick
The very early decisions about the building’s overall form and orientation will have fundamental implications for facade design and performance. Optimising the orientation and layout can reduce the extent and weight of the facade, affect the need for shading and weather protection, and facilitate selection of appropriate cladding and finishes.
There are always options to be rationalised and considered. Profiled claddings can be flattened to reduce material volume; structural slab edges left exposed; spacing of support framing studied to find efficiencies; standard typologies or modular solutions utilised to reduce waste and manufacturing load; and trends or purely aesthetic design elements looked at through the lens of environmental impact.
Greener procurement options are worth considering too. While lower carbon local and/or responsible procurement might cost more initially, strategic procurement – such as bulk purchasing or long-term contracts – may help to mitigate some of the costs.
Substitute, explore and lead with materials choices
An obvious intervention in the embodied carbon equation is selecting lower carbon materials. But like anything in the built form, one decision or change can result in a cascade of other changes and considerations that affect all disciplines. The design team will benefit from working closely with quantity surveyors to identify the carbon reduction options that provide the best value for cost.
Developing an understanding of how various materials can impact costs and carbon is key. This knowledge, along with full lifecycle costing and lifetime carbon analysis, is essential for ensuring that developments stack up in the long term.
Lower-carbon materials such as cross-laminated timber (CLT), recycled metals, low-carbon concrete and low-emission glass are becomingly increasingly viable and available. However, despite traditional materials like concrete, steel and glass being known for their high carbon footprints (largely due to energy-intensive manufacturing processes), they’re also cost-effective, durable, strong, largely recyclable, and help achieve other performance requirements associated with thermals, fire performance and natural light.
Keep an eye on innovation
Smart facades incorporating electrochromic glass, bio-reactive energy systems, dynamic shading and integrated photovoltaics are slowly moving into the limelight. While they’re currently more expensive than traditional materials, their advantages in reducing operational emissions and energy expenses may get them across the line in a business case that puts a premium on sustainability – especially when considering the significant cost of electricity.
Alongside high-tech innovations, a growing number of smart solutions are emerging in the market every day like materials utilising hemp or old clothes, lightweight secondary skin retrofits, and films – and a plethora of existing manufacturers are recycling more, powering with renewables, and procuring responsibly, which will facilitate benefits for everyone.
Innovation in processes is important too. The uptake of digital technologies such as BIM, digital twins and advanced data analytics makes it easier and more efficient to explore carbon options and implications and to test alternatives.
Collaborate for progress
No single role in the building industry will be able to solve the embodied carbon challenge alone – but each discipline can add a unique perspective. It’s time to educate ourselves and join in the carbon conversation to share the learnings, so the building industry can work together towards solutions that will shape a more sustainable future.
About the author
Imogen Lyons is WT’s Carbon Management Lead. Since starting in the industry in 2006, Imogen has worked on various industry leading projects across Australia and Asia. Her experience in carbon management spans various government and private sector developments including high rise student accommodation, build-to-rent towers, office buildings, retrofit / refurbishment developments and airport infrastructure. She is a passionate advocate for innovation, sustainability and believes that today’s buildings and infrastructure shape tomorrow’s world.