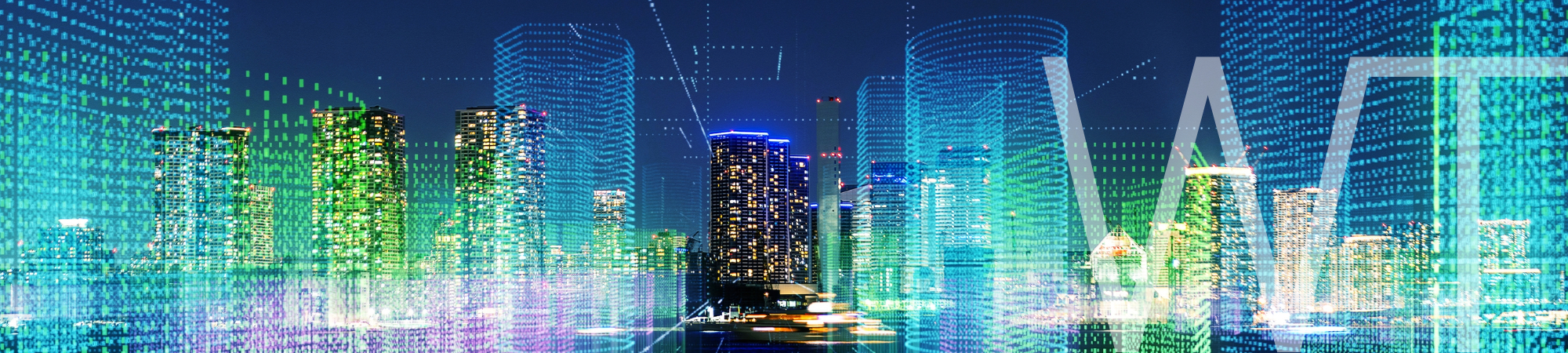
There’s been plenty of hype across many sectors about digital twins, but parts of the construction industry have been somewhat slow on the uptake. This is set to change over the next decade as everything that can be digitised transforms into usable data. Quantity surveyors have an opportunity to become leaders in this arena if we’re willing to grasp it.
The relationship is a natural fit, given that quantity surveyors have always been in the information and data game. Digital twins can be the next chapter in our journey to create insight and deliver value.
Digital reflection magnifies the physical world
A digital twin is an immersive and interactive virtual environment where everyone involved in a project can visualise the asset or structure within its surroundings and investigate it from multidisciplinary perspectives. Sophisticated digital twins also allow real-time monitoring of the built environment and a rich, two-way connection with the physical sibling. When the digital twin incorporates predictive analytics powered by AI and machine learning, it evolves into a ‘cognitive digital twin’ that can react and predict.
As a reflection of a real-world asset, a digital twin allows us to dive deeper into the feasibility of projects at an early stage – helping with cost analysis and scenario planning. During the preconstruction phase it enables quick and visible changes of the evolving design and rapidly reveals the consequent cost implications. It also supports quicker decision making and improved collaboration and transparency among quantity surveyors, architects, planners, engineers, contractors and project owners.
New developments in the industry are overlaying planning and building regulations with digital twins to rapidly assess compliance with quality standards and specifications. One such example is eComply in Victoria.
During construction, the digital twin can reveal the progress of the build. Any errors can be easily documented, monitored, controlled and validated.
Finally, during the post-construction period (operations), the digital twin allows easy assessment of the asset’s current condition and can predict how it will behave over its full lifecycle. This is integral to the costing of maintenance as well as to valuation, insurance, depreciation and overall return on investment.
Even sophisticated BIM models tend to speak to the ‘as-built’ but not to the operational life of the building, so this is a clear differentiator and advantage for the digital twin. The digital twin can also incorporate an entire portfolio – allowing asset management to be planned, coordinated and costed across far more than a single asset.
Digital twins reveal relationships
The digital twin is largely based on rich, multi-dimensional BIM models – which could include a range of dimensions including time (4D), cost (5D), environmental impacts, sustainability and embodied carbon (6D) and facilities management (7D). But it differs from BIM by including much more information about other relationships (the big picture) and by magnifying the real world (the granular detail).
For example, how does the building interact with other buildings around it? Where does it sit in the skyline? What are the ground conditions, subsurface infrastructure and nearby utilities? How vulnerable is the building to climate impacts – whether emergencies such as bushfire and flood, or simply the normal prevailing patterns in temperature and rainfall?
From a cost perspective, the dynamic digital twin can provide more than the static BIM model by accounting for some of these broader contextual factors. For example, how much would it cost to build this building in Perth or in Sydney or even in New York? What do the weather patterns suggest about the timing of the build, progress claims and cashflow progress?
Quantity surveyors and digital twins are in for the long-haul
It’s never too early for the quantity surveyor to get on board with the digital twin. This can start at the absolute outset of conceptual design and feasibility, and certainly doesn’t need to end when the building opens for business.
During occupation, information from sensors, cameras, smart meters and other sources within and around the building can feed directly into the twin, enabling it to monitor the building’s current state as well as to detect and even enact opportunities to improve the building’s operations. This two-way connection – in which the building and the twin ‘listen’ and ‘speak’ to each other – will enrich the management of the facility in the long term, enabling more predictive and proactive maintenance strategies and massively reducing the labour and time taken up in activities such as creating and maintaining an asset register and conducting manual inspections.
Future-ready innovation for a better built environment
When we as cost managers use digital twins, our clients will achieve better outcomes from their projects. Getting ahead of the curve now means that we’ll be out ahead when digital twins become less of a ‘nice to have’ and more of the norm.
WT’s digital twin initiative will transform how we deliver for our clients. With ever-evolving technologies at our fingertips, we will have more capacity to advise and support our clients as we work together to develop better built environments for communities. It’s a leap into a bright and connected new world.
About the author
Dr Cristobal (Cris) Sierra is a Digital Engineer at WT in Australia. Cris is a Mechanical Engineer with a PhD in infrastructure focusing on the adoption of transformative technologies. As a recipient of an Australian Research Council scholarship, he undertook research on the applications of a cognitive digital twin on transport infrastructure. Cris specialises in data visualisation, bringing a wealth of expertise in augmented reality, virtual reality, photogrammetry, point clouds and digital twins.